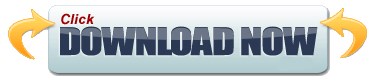
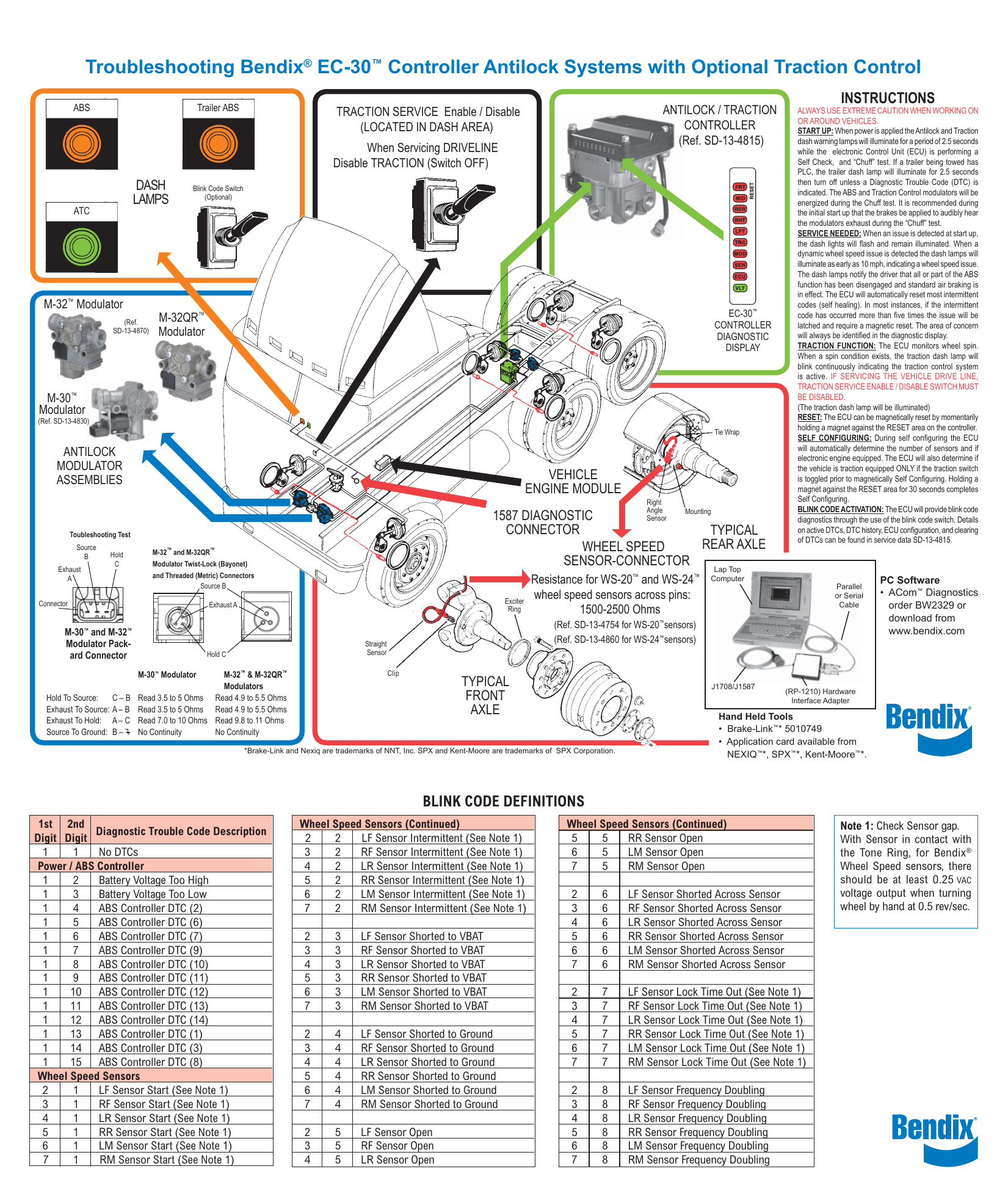
“There are some dash valves that have trip pressures or pop pressures, and if those pressures are incorrect, it’s pretty apparent when you push or pull them,” Sheehan said.
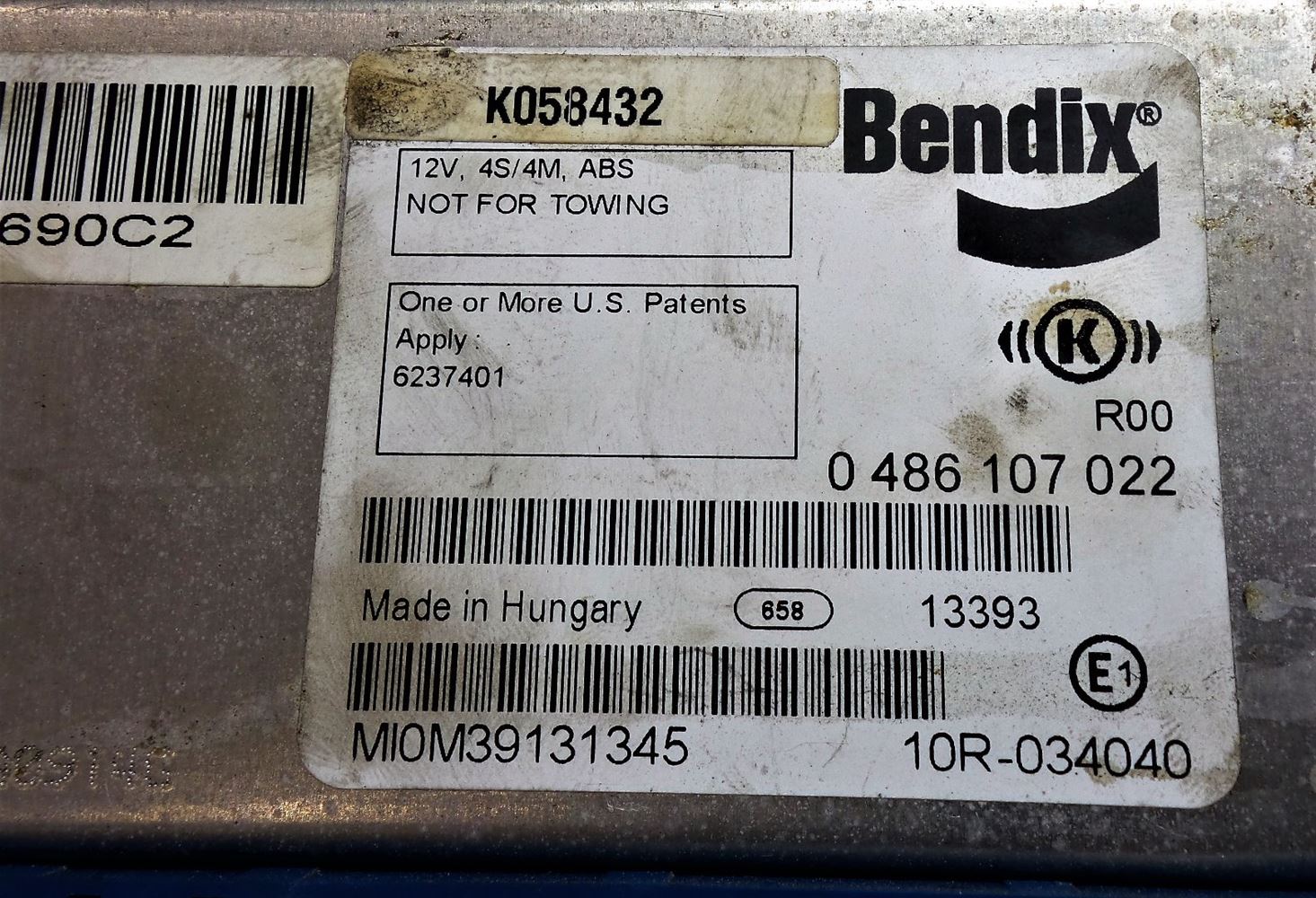
In other cases, the evidence could be right at the driver’s fingertips, or just beneath their feet. “Closer examination using a bubble solution on the suspected leak area can help pinpoint leaks, and the size and frequency of the bubbling will help determine the severity.” “The most common customer concern with valves is leakage, which could be noticed through an audible air hiss,” he said. With a wide variety of valve types and applications in a connected air system, recognizing and diagnosing a valve issue can begin in a number of ways, noted Brian Sheehan, Bendix engineering manager of pneumatic valves. This installment of the Bendix Tech Tips Series focuses on proper troubleshooting, maintenance, and upkeep of valves in a compressed air system.
#BENDIX ABS TROUBLESHOOTING GUIDE DRIVER#
The lesson is: Valves matter to help improve driver safety and comfort.
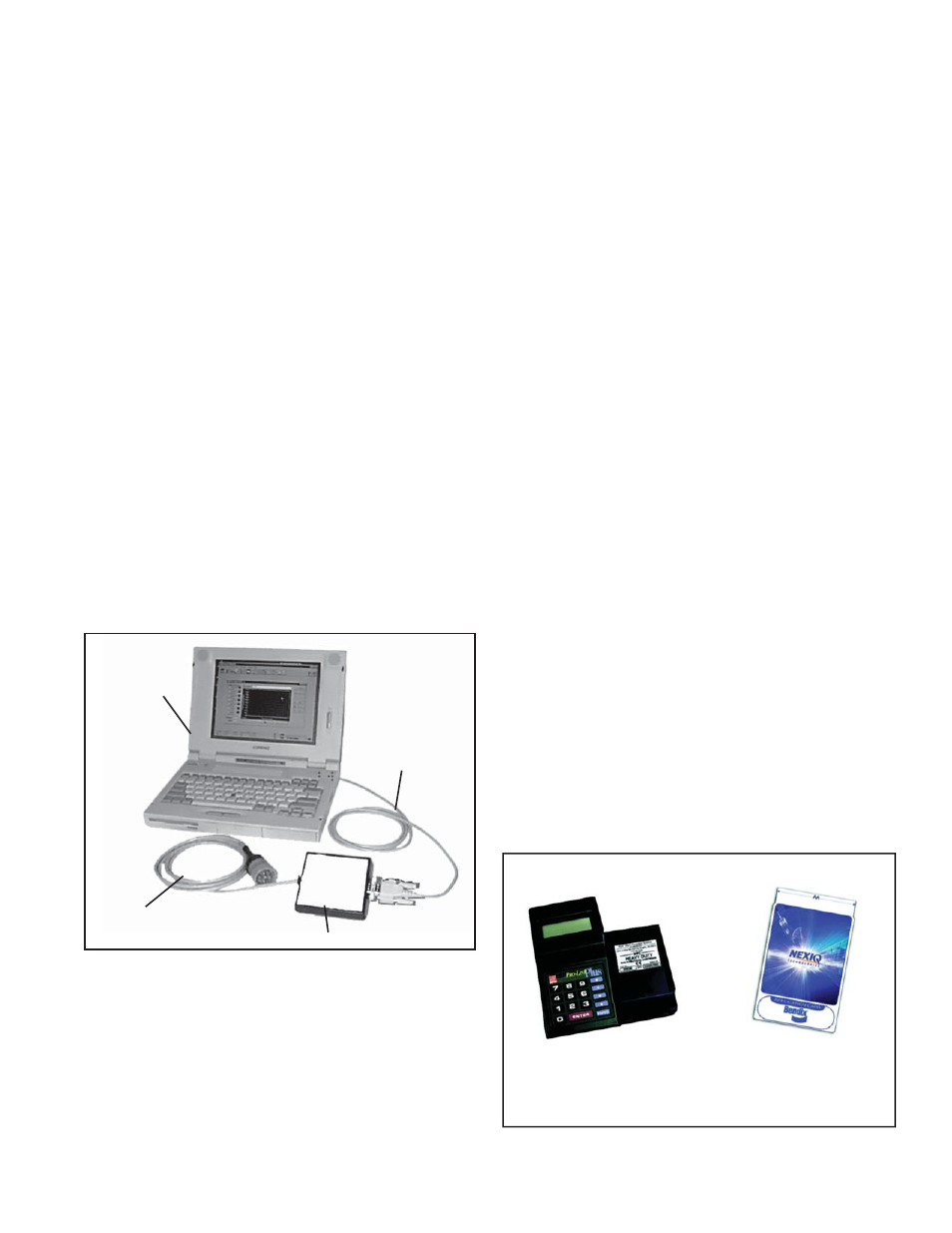
Some automated manual transmissions rely on pneumatic controls, as do emissions controls and other systems. There are often mechatronic components as well, like valves with solenoids used in antilock braking and stability control. And these days, there’s no “typical” air brake system – they can be highly customized with various accessories that use the same compressed air supply, such as lift axles. ELYRIA, Ohio – March 27, 2019 – A typical commercial vehicle air braking system requires at least a dozen core pneumatic valves to meet baseline regulatory standards.
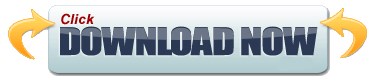